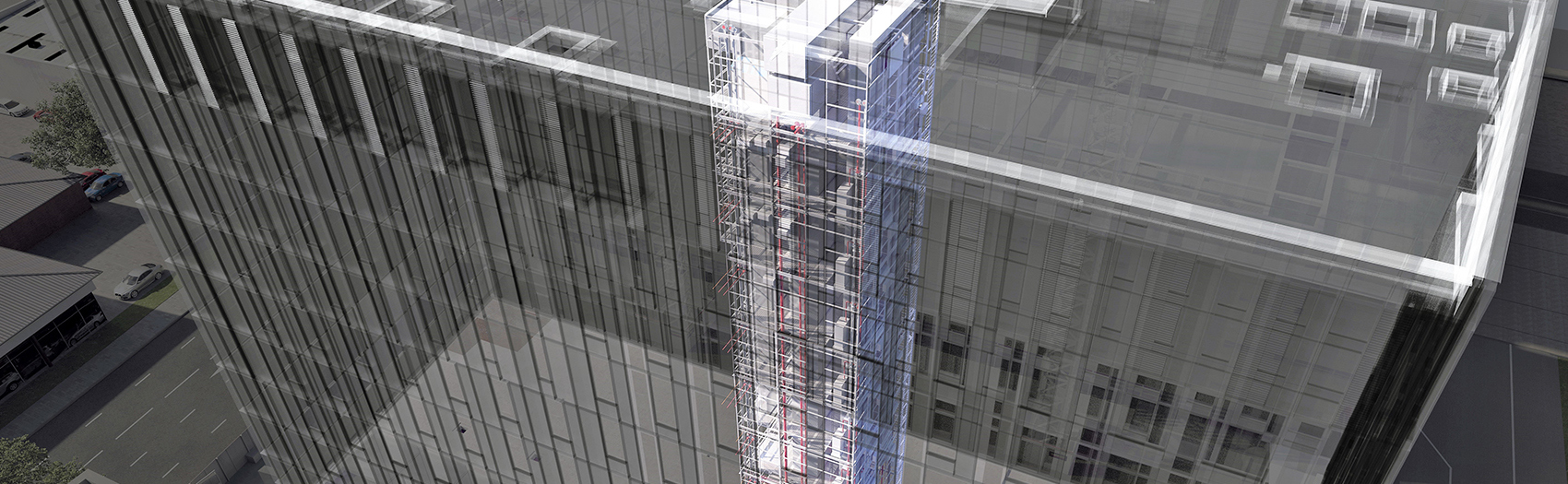
Our offsite journey
Our Design for Manufacture and Assembly (DfMA) techniques have led the field in MEP solutions for three decades, providing DfMA solutions for some of the UK’s most prominent and inspiring projects, transforming them into fast track, sustainable, high performing environments.
Crown House Manufacturing opened to service the refurbishment of the Natwest Tower in London, the success of this innovative solution soon brought about requests from other prominent projects.
Our manufacturing history
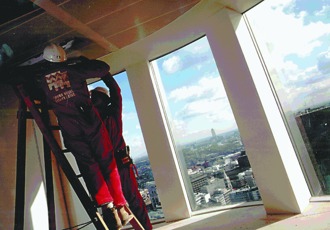
1995 - NatWest Tower, London
Crown House Manufacturing 30,000 Sq ft facility opened to service the refurbishment of the NatWest Tower, London. 800 MEP modules delivered.
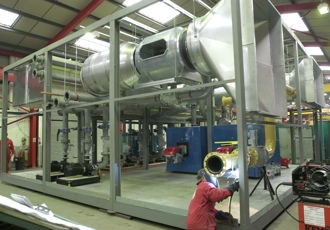
2001 - New facility doubles capacity
Due to unprecedented success and demands, Crown House Manufacturing moves to new 60,000 Sq ft facility, doubling capacity.
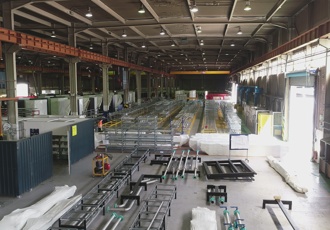
2012 - New facility opens
New 129,000 Sq ft facility opens in Oldbury, doubling capacity again to keep up with the demands for our multiple award winning offsite MEP solutions.
2000 - 2011
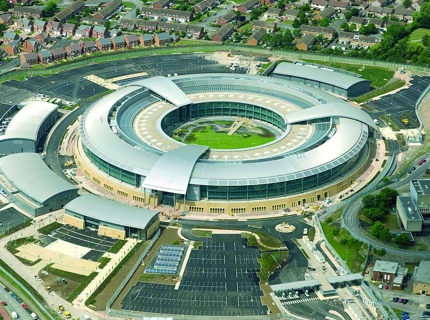
2000 - GCHQ, Cheltenham
Our offsite facility manufactured whole multi-service risers and complete plant modules, which were tested and run in the factory before delivery to site.
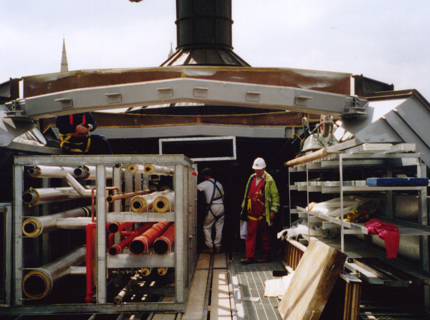
2000 - Portcullis House, London
Due to design constraints and the location of the site, the majority of services were manufactured and pre-assembled off site at CHtM.
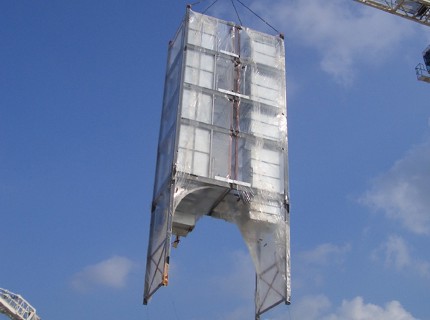
2005 - Royal Ascot Grandstand
CHt heavily utilised its offsite capability for this project – manufacturing an unprecedented 80% of the primary services off site. CHtM manufactured over 600 MEP modules, including 40m vertical risers built in the factory with all services pre-commissioned, installed in one large pre-assembled module.
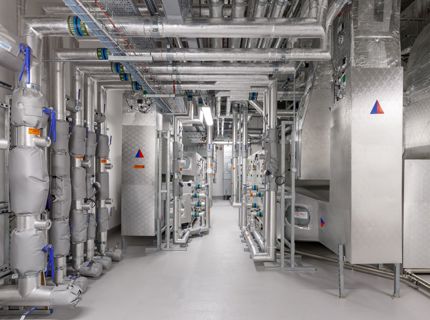
2005 - North Staffordshire Hospital
CHt developed the Assembling, Transporting and Installing framework system (ATIF) using 20 ATIF frames to deliver and install 300 modules saving 280 steel frames, installing six weeks work in just one week for corridor modules.
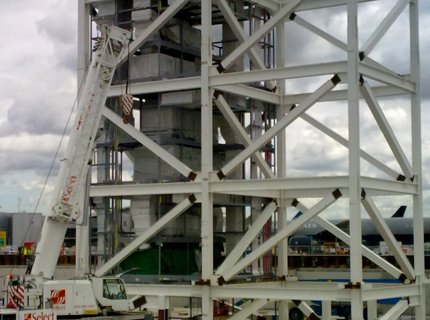
2010 - Queen’s Terminal, Heathrow
12 risers, each measuring 9m x 9m x 40m, were integrated into the installation of the steel frame, with each riser (consisting of 25 modules) weighing approximately 40 tonnes. The risers formed the main mechanical service cores, CHtM also manufactured over 3,000 MEP distribution modules incorporating all containment distribution systems.
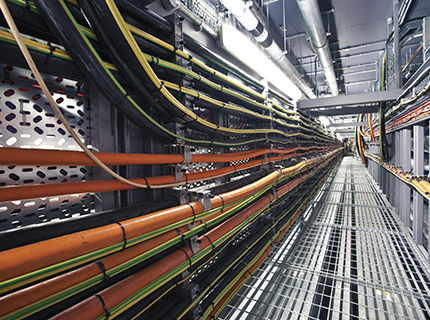
2010 - One Hyde Park
Works included the offsite modularisation of the main risers feeding the four pavilions, risers were transported to site in 12–14m sections and craned into final position within an hour.
2012-2022
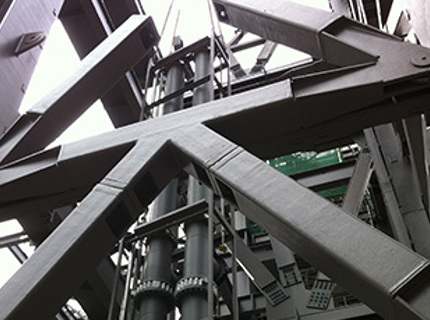
2012 - Leadenhall building, London
Risers were delivered in 12m sections across east, west and north core, the north core service 'tables' were delivered with the building structure, along with 45 on-floor plantrooms that were fully completed including control wiring and lighting, all pre-tested before delivery to site. The main primary system pump modules were in excess of 18 tonnes, with the average riser or on-floor plantroom weighing 6 tonnes.
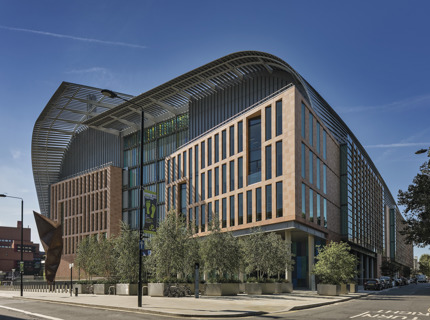
2013 - Sir Francis Crick Institute
4,600 modules of varying sizes and weights up to a maximum of 27 tonnes were delivered and installed.
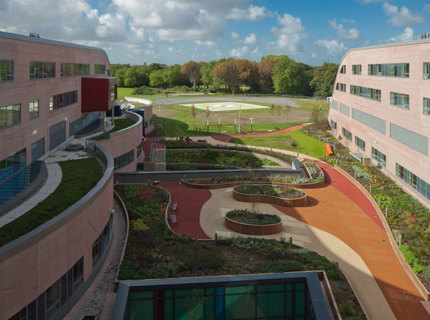
2014 - Alder Hey Children's Hospital, Liverpool
This project was completed 20% faster than predicted using Design for Manufacture and Assembly (DfMA), with 10,000 hours saved on site by using modular services, including MEP modules and bathroom pods.
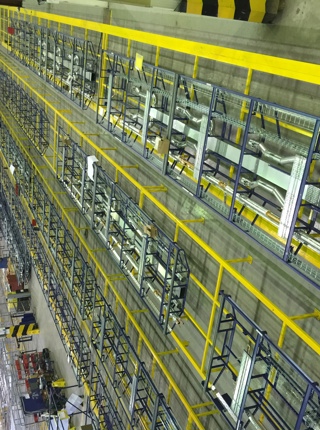
2015 - HMP Berwyn, Wrexham
The first cell risers developed and manufacturing for HMP Berwyn, in Wrexham North Wales, with 924 service modules manufactured and delivered in total, the success of these products leading the way for multiple repeat orders over the subsequent years within the custodial sector.
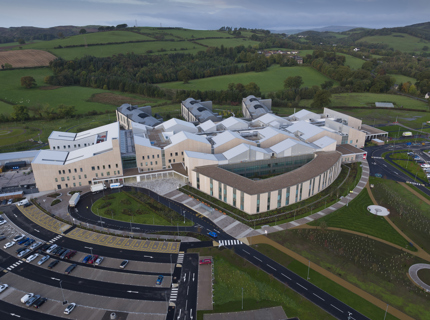
2016 - Dumfries and Galloway Royal Infirmary
1,000 modules containing primary runs of MEP services, and 6,561 primary structural components, all manufactured off site and delivered to site for assembly - Our solutions helped to deliver this new hospital five months faster than could be achieved with traditional methods.
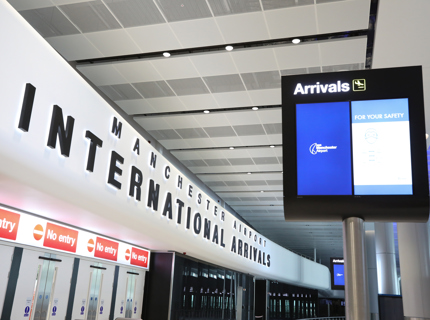
2017 - Manchester Airport Transformation Programme
Our Mega riser solutions were made up of 48 multi-service risers containing ventilation, ductwork, water piping, electrical containment and heating services. A modular energy centre housing three boilers, pumps, DHW generation / storage, controls, wiring and a CHP unit was also installed on site in just two days, delivered in five sections complete with cladding and roofing aligned to architectural requirements.
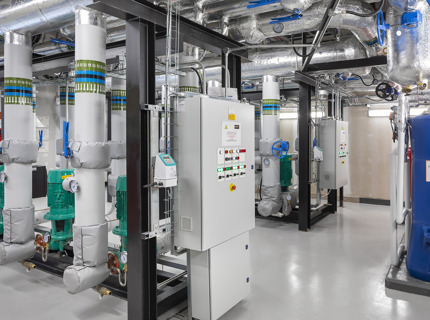
2019 - The Grange University Hospital
A 23% programme saving was secured by using DfMA components. Prefabricated elements included, MEP service risers, MEP service horizontal modules, AHUs and plant skids.

2022 - Future Olympia
An ideal showcase of CHt’s DfMA capabilities, the five storey self-contained Olympia Energy Centre building contains Chillers, Boilers, CHP engines, and all the associated pump sets, pipework, ancillaries and electrical switchgear, It includes four plant skids, multiservice risers, 18 modules, 14 frameless modules, three valve frames and 300 loose spools.