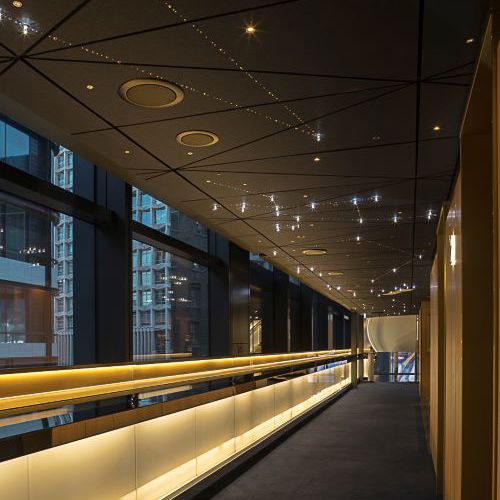
At a glance
Client/project partners: Derwent London
Status: Complete
Location: London
Awards
- Achieved BREEAM Excellent
- Achieved LEED Gold
- Handing-over without defects
- James Collins won Commissioning Manager of the Year for his work at Soho Place
Situated directly above Tottenham Court Road station, the Soho Place development presented numerous technical challenges due to its central location, stringent acoustic requirements and glass-clad beacon design. The 285,000ft² development comprises a 10-storey building with retail and office space, coupled with a nine-storey building split into three office floors above a 600-seat theatre for Nica Burns of Nimax, the first to be built in the West End of London for over 50 years.
This new, 600-seat, in the round auditorium is flexible and required high-performing acoustic features. CHt met this specification through a combination of modern methods of construction, digital engineering and engineering excellence.
Drawing on our previous experience of working with Derwent London we were able to push the boundaries of modern methods of construction, embedding a Design for Manufacture & Assembly approach from the outset.
Complex engineering
The development also brought several technical challenges stemming from its central location, stringent acoustic requirements, the interface with Tottenham Court Road station’s tunnels in the north basement and the Crossrail tunnel in the south basement.
Digital coordination and collaboration to drive certainty
The mixture of retail, commercial and theatre space demanded an integrated approach to meet the specification, especially the soundproofing and acoustic requirements of the theatre.
CHt deployed our industry-leading BIM experts to produce and interrogate an ‘as-built’ model of the design, allowing us to identify risks and opportunities, enhance quality at an early stage, and inform cost allocation, in turn driving cost and programme certainty.
We also held regular collaboration sessions with the client, novated design team, external subcontractors, and internal manufacturing –conducting 3D sequencing simulations and ‘walkthroughs’ of the digital model – to achieve a right-first-time, defect-free build.
We saved time on the build programme by manufacturing off site and we were able to improve product quality, reduce waste and use a more diverse and digitally skilled workforce.
Bringing constellations to Oxford Street
Derwent London had exacting requirements that even extended to internal lighting. In the auditorium space, their vision required 30+ different luminaire manufacturers to achieve the desired aesthetic. Our team, took responsibility and sought a solution for standardising the luminaire brightness regardless of manufacture. We achieved this by reviewing the grouping method of lights and, instead, utilised the built-in scene recall features of each luminaire. This gave the level of control and ease of operation of each luminaire. Furthermore, through the construction phase, we installed architectural lighting to mimic stat constellations that were visible to the public on the street below during both the day and night. We achieved this finish through an IP back bone and DALI pair per circuit to enable future FM teams to quickly adapt the system to make changes visible without removing the ceiling void or major rewiring.
The lighting has given Soho Place a unique aesthetic that can be enjoyed by both building users and passers-by.
Added value to clients:
- Full coordination of details in a digital environment, supporting pricing and buildability
- Reduced onsite labour, increased quality and lower programme risk through offsite prefabrication
- We engaged early with client commissioning experts and our in-house commissioning leaders/subcontractors to develop the designs to de-risk the back end of the programme. Installation was managed by our experienced construction managers. We used the Field View electronic quality management system to support effortless handling of defects, inspection and test plans, and witnessing.
- In-house commissioning managers re-joined the project part-way through to spearhead the commissioning programme.
- 115m2 of solar PV panels providing onsite source of renewable energy
- The building will be supplied by renewable electricity and gas
- Greywater from the building will be recycled
- Enhanced sub-metering will enable tenants to monitor their electricity consumption
- The embodied carbon emissions of the building will be offset using verified schemes
- BREEAM Outstanding (NC 2014)
- LEED Gold (v4)
Components manufactured offsite
“It was a privilege to work with an incredibly talented team and our committed supply chain partners to deliver an exemplar and technically challenging project. ”