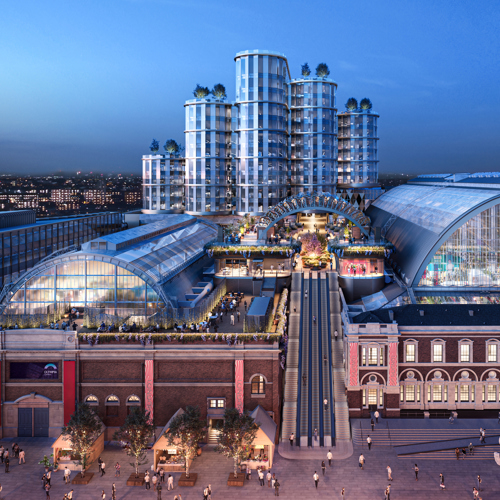
At a glance
Client/project partners: Yoo Capital and Deutsche Finance International
Duration: Live
Location: London
Work includes revamping the existing exhibition halls and adding 51,000m² of office, studio and co-working space, a four-screen cinema, 4,000-seat venue, 1,500-seat theatre, 900m² of performance space, new hotels, and new restaurant, retail and public realm space – all to be achieved while exhibition areas remain operational.
Early engagement and collaboration with the client, design team and other delivery partners has been vital to the success of the project and has enabled all parties to agree a DfMA-led design.
Our DfMA solution means that the majority of the project is manufactured offsite, which has health and safety benefits as well as providing the client with greater certainty of programme and cost, whilst also ensuring the quality of what’s delivered.
Complex engineering
As part of the wider Olympia development, we were required to undertake diversion/extension works to a range of operationally sensitive MEP systems across 34,000m2 of events space.
Space is as always at a premium, particularly when referring to the non-lettable space used for MEP plant areas. To assist with all of these requirements our team used advanced Digital Engineering capabilities to ensure that the most efficient designs have been implemented is neatly squeezed within the restricted Energy Centre footprint.
The beating heart
The five storey self-contained Olympia Energy Centre building containing Chillers, Boilers, CHP engines, and all the associated pump sets, pipework, ancillaries and electrical switchgear, is an ideal showcase of CHt’s DfMA capabilities. It includes four plant skids, multiservice risers, 18 modules, 14 frameless modules, three valve frames and 300 loose spools.
One of the key challenges of the Energy centre project was that we were required to ensure that all event spaces (both front and back of house) remained operational during construction works. ‘Operational’ was defined as being thermally comfortable, adequately illuminated, and safe.
We used digital scanning to ensure that the dimensional constraints were properly imported in the design model to ensure spatial fit, methodology related constraints were thoroughly integrated prior to executing the works. This method and approach drove innovative thinking, an example of which is the de-commissioning of the existing chilled water system and associated sub-stations, while still maintaining adequate cooling to the event space.
Our digital and DfMA approach ensured that the works were delivered to time and budget with minimal operational impacts on our client's event business, while overcoming significant resource challenges during the pandemic.
“The skill and determination shown by all involved is quite remarkable. An integral plantroom with a typical 25 week installation programme with a static weight of 5000kg a section, delivered and installed defect free in 4 days! ”